Visual Abstract
Abstract
This research delves into the comprehensive exploration of silica nanoparticles (SiO2-NPs) synthesis via ultrasonic spray pyrolysis. Essential factors investigated encompassed varying concentrations of tetraethyl orthosilicate (TEOS) (0.51 M, 0.25 M, and 0.12 M), furnace temperatures (200°C, 300°C, and 400°C), carrier gases (Ar, N2, O2), residence times of reactants in the furnace (0.5 sec, 1.5 sec, 5 sec), and solvents (acetone, ethyl acetate, and ethanol). The influence of incorporating F127 in the synthesis process was scrutinized for its role in producing mesoporous silica nanoparticles. Results indicated that an escalation in TEOS concentration from 0.12M to 0.51M at 400°C resulted in a proportional increase in the average particle diameter of SiO2 nanoparticles from 7 nm to 40 nm and the specific surface area decreased from 147 to 97 m2/g, revealing a narrow size distribution. Manipulating the nitrogen flow rate during the furnace process from 100 to 300 ml/min exhibited the capability to yield SiO2 nanoparticles by increasing their particle size to 61nm. Additionally, an extension of the residence time of precursors, achieved through careful regulation of the carrier gas flow rate, yielded a noticeable augmentation in the average particle diameter. Notably, the choice of solvent emerged as a discernible factor, leading to the fabrication of SiO2-NPs with various morphologies. This multifaceted investigation provides valuable insights into the intricacies of silica nanoparticle synthesis, contributing to the understanding of the nuanced interplay of parameters in achieving desired particle characteristics for diverse applications in nanotechnology and materials science.
Introduction
Nanoparticles, defined as particles with dimensions on the nanometer scale, have emerged as pivotal entities in the realm of materials science, exhibiting unique and size-dependent physicochemical properties [1]. In addition, nanoparticles due to their diminutive size, exhibit distinctive and significant properties that set them apart from bulk materials. The most notable feature is their remarkable surface area-to-volume ratio. As the particle size decreases, the proportion of atoms or molecules located at the surface becomes dominant, leading to an increased surface area per unit mass [2]. This property amplifies the reactivity of nanoparticles, making them highly efficient in various applications. The significant properties of nanoparticles, including their high surface area, quantum effects, and diverse compositions, make them pivotal in a wide array of applications, from medicine to electronics, catalysis to environmental science. Understanding and harnessing these properties continue to drive advancements in nanotechnology and its myriad possibilities for innovation [3].
Nanoparticles’ diverse compositions, encompassing metals, metal oxides, polymers, and more, contribute to their versatility [4–6]. Silica nanoparticles, characterized by their composition of silicon dioxide (SiO2), have emerged as a focal point in nanomaterial research due to their unique properties and versatile applications [7]. The inherent biocompatibility and low toxicity of silica nanoparticles make them particularly attractive for biomedical applications. In drug delivery, silica nanoparticles serve as efficient carriers, allowing for controlled release and targeted delivery of therapeutic agents [8]. Their tunable surface chemistry enables functionalization with various ligands, enhancing the nanoparticles’ affinity for specific cells or tissues [9]. Moreover, silica nanoparticles have found utility in imaging and diagnostics, where their optical properties can be exploited for contrast enhancement in techniques such as fluorescence imaging and magnetic resonance imaging (MRI) [10,11]. Beyond medicine, silica nanoparticles exhibit excellent thermal and chemical stability, making them valuable in catalysis and sensing applications [12]. Their porous nature allows for high surface area, facilitating the adsorption of molecules and catalytic reactions. Additionally, silica nanoparticles are employed in environmental remediation, acting as efficient adsorbents for pollutants [13]. This academic exploration delves into the myriad benefits and applications of silica nanoparticles, shedding light on their potential contributions across diverse scientific domains.
The synthesis of silica nanoparticles encompasses a spectrum of methods that cater to the precise control of particle size, morphology, and surface properties. One of the widely employed techniques is the Stöber process, a sol-gel method that involves the hydrolysis and condensation of tetraethyl orthosilicate (TEOS) in the presence of a surfactant, resulting in monodisperse spherical nanoparticles [14,15]. The microemulsion method utilizes surfactant-stabilized oil-in-water emulsions for controlled nanoparticle formation. Alternatively, the reverse microemulsion technique produces smaller-sized silica nanoparticles with enhanced surface area. The sol-gel method, incorporating various precursors such as TEOS or sodium silicate, remains a versatile approach allowing for the synthesis of silica nanoparticles under mild conditions [16]. Additionally, the template-assisted method involves the use of sacrificial templates, such as block copolymers or mesoporous materials, to create well-defined structures. Each synthetic method confers specific advantages in tailoring the properties of silica nanoparticles, offering researchers a diverse toolkit to address the requirements of various applications, from drug delivery systems to catalysis and beyond. The nuanced understanding and optimization of these synthetic strategies play a pivotal role in advancing the field of silica nanoparticle research [17].
Ultrasonic spray pyrolysis stands out as a notable method for the synthesis of silica nanoparticles, combining the principles of ultrasonic atomization and pyrolysis [18]. In this process, a precursor solution containing a silica source, often tetraethyl orthosilicate (TEOS), is subjected to ultrasonic waves, leading to the formation of fine droplets. These droplets, entrained in a carrier gas, are subsequently directed into a high-temperature chamber where the precursor undergoes pyrolysis, resulting in the formation of silica nanoparticles [19]. This method offers several benefits, including precise control over particle size and morphology due to the fine atomization achieved by ultrasonic waves [20]. The versatility of ultrasonic spray pyrolysis allows for the synthesis of monodisperse nanoparticles with a narrow size distribution. The process is also amenable to scale-up, making it suitable for large-scale production [21]. In nanotechnology, the silica nanoparticles produced through ultrasonic spray pyrolysis find applications across diverse domains. They are particularly relevant in catalysis, where the controlled synthesis allows for the creation of high-surface-area catalysts [22]. Furthermore, their tunable properties make them valuable in drug delivery systems, sensing applications, and as constituents in composite materials. The combination of precision, scalability, and adaptability positions ultrasonic spray pyrolysis as a compelling method for the synthesis of silica nanoparticles, contributing significantly to the advancement of nanotechnology [18].
This methodology affords the opportunity to exert precise control over a multitude of parameters, including ultrasonic amplitude, precursor solution composition, flow rate, deposition temperature, and substrate temperature [23]. The ultrasonic spray pyrolysis process involves a sequential series of four key steps: (1) the generation of droplets derived from a precursor solution, (2) subsequent reduction in droplet size through evaporation, (3) conversion of the precursor into oxides, and (4) the ultimate preparation of nanopowders [24]. Within this framework, both organic and inorganic salts emerge as viable precursors for the fabrication of metallic nanoparticles, nanocomposites, and metal oxides. Categorically, ultrasonic spray pyrolysis-synthesized powders can be delineated into three groups, encompassing (1) metals such as Au, Ag, Co, Cu, Zn, Ni, Fe; (2) metal oxides including TiO2, ZnO, YSZ, In2O3; and (3) composite materials characterized by a core-shell structure, exemplified by Li1.6Mn11.6O4, FeCo, FeNi, Ag/TiO2, Au/TiO2, Ni/Ti, Ni/TiO2 [18, 21, 24-29]. The resultant size distribution of the nanoparticles is contingent upon both the atomized droplet size and the initial concentration of the precursor solution. The size and morphology of the produced nanoparticles are intricately linked to the concentration and velocity of the droplets generated by the atomizers. In the realm of spray pyrolysis studies, diverse atomization methods have been employed, including air-assist (pneumatic) or two-fluid nozzles, ultrasonic, vibrating orifice, and spinning disk mechanisms [30].
This research endeavors to produce SiO2 nanoparticles employing a cost-effective and straightforward synthesis method. The investigation delves into the influence of surfactant type, temperature variations, precursor concentration, and solution flow rate on the nanoparticle synthesis process. The outcomes reveal the successful fabrication of SiO2 nanoparticles exhibiting cubic, spherical, and ultra-pure characteristics, a determination validated through thorough characterization using advanced techniques such as Field Emission Scanning Electron Microscopy (FE-SEM), Fourier Transform Infrared Spectroscopy (FT-IR), and Brunauer-Emmett-Teller (BET) analysis. These methodologies collectively contribute to a comprehensive understanding of the synthesized SiO2 nanoparticles, elucidating their morphological, structural, and surface properties.
Experimental
Materials and Method
All materials and solvents, including Tetraethyl ortho silicate (TEOS 40 WN), ethanol, acetone, and ethyl acetate, were procured from Merck (Germany), while Pluronic F–127 was synthesized from Sigma. The identification of the as-prepared nanoparticles and the characterization of silica nanoparticles were conducted using FT-IR spectra (Rayleigh WQF–510A). Morphological examination and determination of the average particle diameter of silica nanoparticles were performed through Field Emission Scanning Electron Microscopes (FE-SEM), utilizing ZEISS FOS-UT and MIRA3 TESCAN instruments. The BET surface area (SBET) of the samples was ascertained from N2 adsorption-desorption isotherms acquired at 77 K using a Surface Area Analyzer (Micromeritics Instrument, USA). Before measurement, all samples underwent a 2-hour outgassing at 473 K, and 0.1 Pa. Surface areas were computed using the Brunauer–Emmett–Teller (BET) method. Elemental information was obtained through Energy Dispersive Analysis of X-rays (EDAX). Thermal analysis of the synthesis process was executed using a Hunyung px9 furnace with an adjustable temperature of up to 1100°C.
Synthesis of SiO2 nanoparticles
The TEOS served as the precursor for the creation of three distinct solutions containing varying concentrations of SiO2 (0.51, 0.25, and 0.12 M), dissolved in ethanol as the suitable solvent. The addition of F127 was implemented in the 0.51 M SiO2 solution, and an examination of surfactant effects was conducted in both its presence and absence. Varied solvents, including ethyl acetate and acetone, were employed in the preparation of different silica solutions, prompting an investigation into their influence on morphological outcomes. The experimental setup comprised an ultrasonic atomizer for aerosol precursor generation, a quartz chamber functioning as a furnace, and a particle collector. The ultrasonic vibrator (1.7 MHz) facilitated the atomization of the TEOS solution, and the resulting droplets were subsequently transported into the central tube of the furnace using flowing dry gases—Ar, N2, and O2—at different temperatures. The nanoparticles generated through Ultrasonic Spray Pyrolysis were collected on the surface of a cold quartz tube.
Results and Discussion
Several factors exert influence on the average particle diameter, specific surface area, and morphology of SiO2 powder. These factors encompass the concentration of Tetraethyl silicate (TEOS) at levels of 0.51, 0.25, and 0.12 M, diverse furnace temperatures set at 200, 300, and 400°C, the use of different carrier gases (Ar, N2, O2), varying residence times of reactants within the furnace (0.5, 1.5, and 5 sec), and the utilization of distinct solvents (acetone, ethyl acetate, and ethanol), along with F127 as a surfactant. The investigation of these parameters is integral as they serve as significant experimental variables for precisely controlling both particle morphology and average particle diameter in the synthesis of SiO2 nanoparticles.
Effect of different solvents
Ethanol, acetone, and ethyl acetate were used as solvents. The effect of solvent variation on particle diameter, specific surface area, and their morphology was investigated and the obtained results are shown in Table. 1. Moreover, nitrogen adsorption-desorption data are illustrated in Fig 1 (a, b, and c). In addition, Fig 1(d, e, and f) shows SEM images of SiO2-NPs prepared in acetone, ethanol, and ethyl acetate, respectively. It is obvious that morphologies of nanoparticles are spherical and like the results obtained from BET analysis in Table. 1, SEM images also confirm that the particles prepared in ethanol have smaller sizes. Certainly, the synthesis with ethyl acetate solvent shows the tendency to change the morphology of the particles from spherical to cubic.
Solvent | BET surface area (m2/g) | Adsorption average pore diameter (nm) | Average particle size (nm) |
Ethanol | 97.68 | 20.17 | 61.42 |
Acetone | 17.02 | 5.90 | 352.49 |
Ethyl Acetate | 10.34 | 13.6 | 580.25 |
FT-IR spectroscopy is well known as a helpful and applicable technique to understand the functional group of any organic molecule. The IR spectra of SiO2 NPs are presented in Figure 1 (g). The FTIR spectra of silica nanoparticles commonly display significant absorption peaks within the 400–1000 cm−1 range, attributed to the stretching vibrations of Si-O-Si bonds, alongside peaks in the 1400–1600 cm−1 range, indicative of the bending vibrations of Si-O-Si bonds. In addition, The IR spectrum of the silica nanoparticles prepared in acetone as solvent shows absorption peaks around 1550–1650 cm–1, 1350–1400 cm–1, and 1049cm–1, which are due to the C = O stretching vibrations, methyl group and C-O vibrations, respectively. The samples fabricated in ethyl acetate solvent show absorption peaks at 1650, 1049, and 2981cm–1, which are due to the C = O, C-O, and the alkyl group vibrations, respectively. In the case of the silica nanoparticles prepared using ethanol as solvent, the IR spectrum shows absorption peaks at 1442 and 1573 cm–1, and two small strips at 2854, and 2925 cm–1, which are due to the C-O vibrations, and alkyl group vibrations, respectively [31, 32].
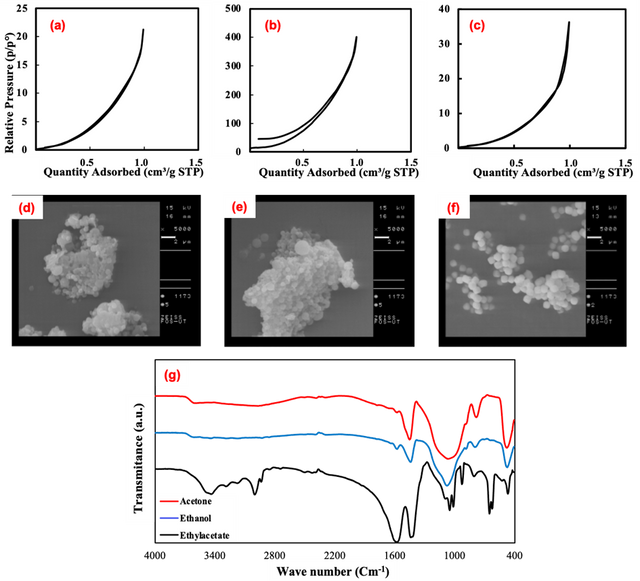
Effect of Tetraethyl Silicate Concentration
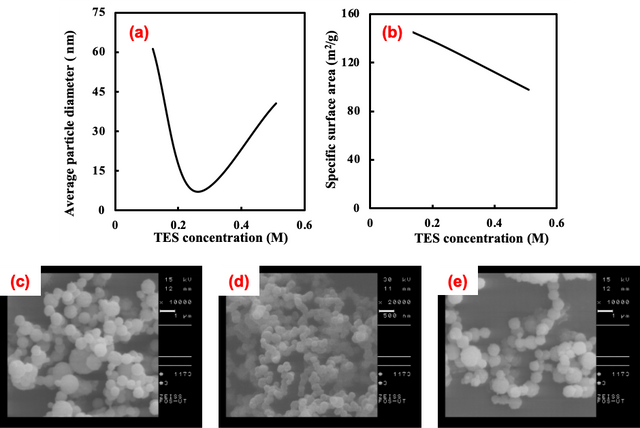
Effect of Temperature
To investigate the effect of maximum furnace temperature on particle size, the rate of nitrogen flow in the furnace was changed at the fixed. In this step TEOS concentration was held at 0.51 M and by controlling the rate flow of N2 maximum furnace temperature ranged from 400 to 200°C. Due to the low coalescence rate among small particles at low furnace temperatures, it was expected that the average particle diameter to be smaller by diminishing temperature.
As can be seen in Figure 3, the average particle size increased from 7 to 61 nm. This disagreement could be related to incomplete evaporation of sprayed droplets, since in the short residence times and without further evaporations, larger particles can be formed.
Effect of Residence Time
To study the effect of residence time on the particle size, the rate of carrier gas flow at the pyrolysis tube of the furnace was varied from 300 to 100 ml/min. For this aim, other parameters such as TEOS concentration, flow rates of cold vapor, and the maximum flame temperature (400 °C) were kept constant. By increasing the linear velocity of carrier gas, the residence time of the precursor in the flame will be shorter.
Then it was expected that particle size for the short residence time to be smaller due to a lower coalescence rate among small particles. As the linear velocity of TEOS in the furnace increased, the average particle diameter increased from 7 to 61nm (Figure 4).
Effect of F127 as Surfactant
To examination the effect of surfactant on SiO2 nanoparticles, silica mesoporous nanoparticles was synthesized using F127 as surfactant by ultrasonic spray pyrolysis, so according to the results of BET and SEM analysis for the NPs (Figure 5 (a, b)),, the average particle diameter and specific surface area were obtained 7nm, and 796 m2/g respectively. From BET analysis, it is evident that the sample has typical IV isotherms with H1 hysteresis, representing the formation of the mesoporous sample after calcination. The FTIR spectra of silica nanoparticles typically manifest notable absorption peaks within the 400–1000 cm−1 interval, arising from the stretching oscillations of Si-O-Si bonds, coupled with peaks observed in the 1400–1600 cm−1 region, attributed to the bending vibrations of Si-O-Si bonds. Also, The FT-IR spectrum of the sample prepared employing F127 surfactant, shows a peak at about 2900 cm–1 which is related to stretching modes of aliphatic C-H (Figure 5 (c)).[.[33]
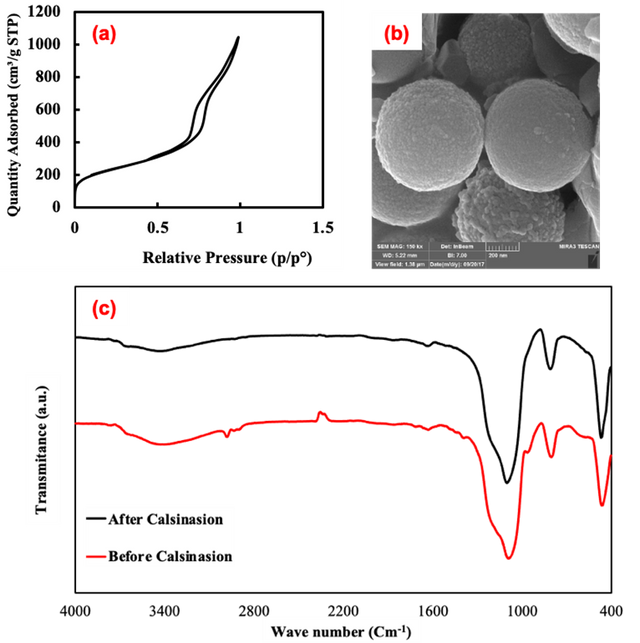
Conclusions
The alteration of solvents from ethanol to acetone and ethyl acetate resulted in significant variations in both the average particle diameter and specific surface area, transitioning from 61 to 580 nm and 97 to 10 m²/g, respectively. Through the ultrasonic spray pyrolysis method, amorphous SiO2 nanoparticles were successfully synthesized with diameters ranging from 7 to 580 nm. Notably, an increase in TEOS concentration in the furnace from 0.12 to 0.51 M led to a proportional rise in the average particle diameter, maintaining a consistently narrow particle size distribution within the range of 7 to 40 nm. Furthermore, the average particle diameter exhibited an increase from 7 to 61 nm as the maximum flame temperature was reduced from 400 to 200 °C by regulating the N2 flow rate. Control over the nitrogen flow rate and the introduction of cold vapor in the furnace resulted in the production of larger particles with a decrease in the maximum flame temperature. The average particle diameter demonstrated a positive correlation with an increase in residence time, controlled by adjusting the carrier gas flow rate. Lastly, the synthesis of silica mesoporous nanoparticles employing F127 through ultrasonic spray pyrolysis yielded particles with uniform spherical morphology and high specific surface area. Analysis using Field Emission Scanning Electron Microscopy (FE-SEM) and Brunauer–Emmett–Teller (BET) revealed an average particle diameter of 7 nm and a specific surface area of 796 m²/g.
Statements and Declarations
Authors' contributions
All authors have the same contribution.
Competing interests
The authors declare no competing interests.
Ethics approval
Not applicable.
Data availability
The datasets generated and/or analyzed during the current study are available from the corresponding author upon reasonable request.
Funding
No funding was received to support this work.
Acknowledgments
The authors express their gratitude to the Sharif University of Technology and the University of Tehran for providing financial support for this research endeavor.
Authors’ Information
Soheil Sojdeh—Department of Chemistry, Sharif University of Technology, Tehran, Iran;
Hossein Daneshgar—Department of Chemistry, Sharif University of Technology, Tehran, Iran;
Alireza Badiei—School of Chemistry, College of Science, University of Tehran, Tehran, Iran;
Mojtaba Bagherzadeh—Department of Chemistry, Sharif University of Technology, Tehran, Iran;
Navid Rabiee—Centre for Molecular Medicine and Innovative Therapeutics, Murdoch University, Perth, WA 6150, Australia.